Las turbinas aeroderivadas, adaptadas de la aviación a la industria energética, ofrecen alto rendimiento, arranques rápidos y eficiencia térmica, siendo clave en sistemas críticos. Para mantener su fiabilidad y vida útil, es fundamental un mantenimiento preventivo que anticipe fallas mediante inspecciones programadas y control técnico riguroso. Dada su operación a altas velocidades y en condiciones térmicas extremas, cualquier descuido puede derivar en fallas costosas. El mantenimiento abarca sistemas como compresor, combustión, lubricación, combustibles y control. Implementar cronogramas adecuados, junto con prácticas operativas eficientes, garantiza continuidad operativa, seguridad y sostenibilidad en la generación energética.
Fecha:Friday 04 Jul de 2025
Las turbinas aeroderivadas son equipos de alta tecnología diseñados originalmente para la aviación, pero adaptadas exitosamente para generación eléctrica y procesos industriales. Su diseño liviano, alta relación potencia-peso, capacidad de arranque rápido y eficiencia térmica las hacen ideales para aplicaciones críticas donde la continuidad del servicio es fundamental. Sin embargo, para garantizar un rendimiento sostenido y una vida útil prolongada, es indispensable implementar un programa riguroso de mantenimiento preventivo, respaldado por cronogramas bien estructurados y buenas prácticas operativas.
¿Por qué es clave el mantenimiento preventivo en turbinas aeroderivadas?
A diferencia del mantenimiento correctivo, que se aplica tras una falla, el mantenimiento preventivo busca anticiparse a los problemas, realizando intervenciones programadas que aseguren el óptimo estado de cada componente antes de que ocurra una avería. En el caso de las turbinas aeroderivadas, esto resulta vital por varias razones:
- Altas velocidades de operación: Los componentes internos operan a miles de revoluciones por minuto, lo que genera un elevado desgaste mecánico si no se controla.
- Condiciones térmicas extremas: La turbina está expuesta a ciclos térmicos severos, especialmente en las etapas de combustión y expansión.
- Aplicaciones críticas: Muchas de estas turbinas se utilizan en hospitales, plataformas offshore, refinerías o plantas de respaldo, donde un fallo implica consecuencias económicas y operativas severas.
Un programa preventivo efectivo no solo mejora la confiabilidad, sino que también reduce costos por paradas no planificadas, extiende la vida útil de la turbina y facilita la planificación de repuestos y recursos técnicos.
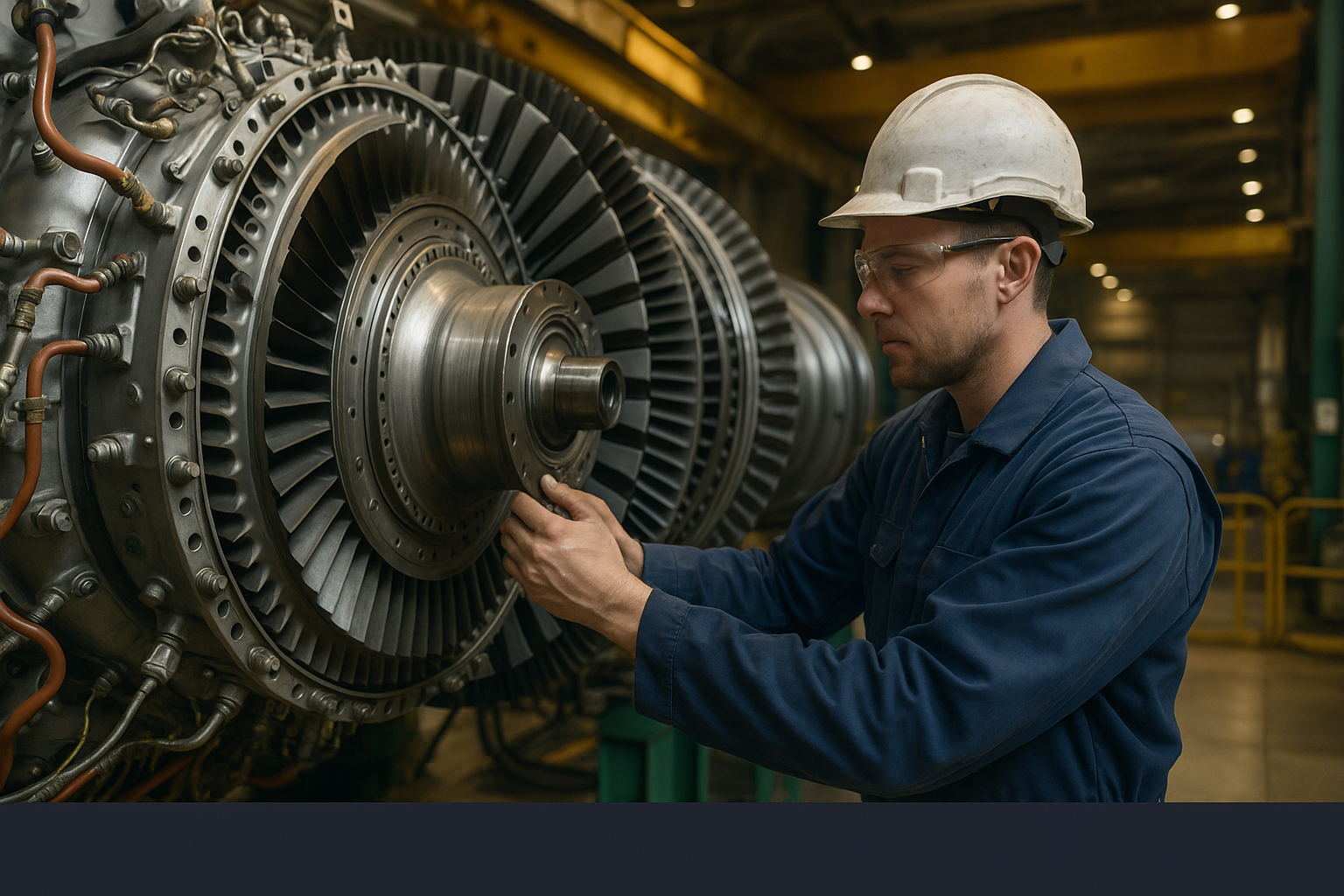
Componentes clave que requieren mantenimiento periódico
El mantenimiento preventivo debe abordar todos los sistemas principales que integran la turbina aeroderivada. Entre los más importantes se encuentran:
- Sistema de ingreso de aire: Inspección y limpieza de filtros, revisión de ductos de entrada y control de partículas contaminantes que puedan ingresar al compresor.
- Compresor axial: Verificación de alineación, desgaste en álabes y sellos, acumulación de suciedad o partículas, y verificación de eficiencia en la compresión.
- Cámara de combustión: Revisión de boquillas, alineación de elementos, verificación de ignitores y análisis de estabilidad de llama.
- Turbina de potencia: Inspección de álabes y discos, control de fisuras por fatiga térmica, lubricación de cojinetes y monitoreo de vibraciones.
- Sistema de lubricación: Cambio de aceite, análisis de partículas metálicas, revisión de bombas, válvulas y sistema de refrigeración.
- Sistema de combustibles (gas natural o diésel): Limpieza de inyectores, control de válvulas de control, pruebas de estanqueidad y eficiencia de mezcla.
- Sistema hidráulico (si aplica geometría variable): Verificación de actuadores, presiones de trabajo, niveles de fluido y funcionamiento de válvulas.
- Sistema de control y monitoreo: Validación de sensores, calibración de transmisores, respaldo de parámetros, y verificación de lógica de protección.
- Generador acoplado (si forma parte del conjunto): Revisión de acoplamientos, aislamiento de bobinas, limpieza del rotor y pruebas dieléctricas.
Cronogramas de mantenimiento: estructura y planificación
El cronograma de mantenimiento preventivo debe estar alineado con las recomendaciones del fabricante (OEM) y ajustado a las condiciones reales de operación. Generalmente, se estructura en tres niveles:
1. Mantenimiento diario o rutinario (visual y básico)
- Verificación de parámetros operativos (presiones, temperaturas, vibraciones)
- Revisión de alarmas en el sistema de control
- Inspección visual de fugas, ruidos anormales o vibraciones excesivas
- Verificación de niveles de aceite y combustible
2. Mantenimiento semanal/mensual
- Limpieza de filtros de aire
- Revisión de válvulas de purga y trampas de condensado
- Descarga de datos del sistema de monitoreo
- Pruebas de funcionamiento de sistemas auxiliares
3. Mantenimiento trimestral/semestral/anual
- Cambio de aceite y filtros del sistema de lubricación
- Inspección boroscópica de compresor y turbina
- Pruebas funcionales del sistema de control y protecciones
- Revisión completa de cámara de combustión e inyectores
- Pruebas de generador (si aplica)
- Validación del sistema hidráulico (si está presente)
Este cronograma debe ajustarse dependiendo del régimen de operación: continuo, intermitente, en espera o de respaldo. También influye el tipo de combustible utilizado y las condiciones ambientales (temperatura, humedad, altitud, presencia de polvo, etc.).
Buenas prácticas operativas para maximizar el rendimiento
El mantenimiento preventivo se potencia cuando se complementa con prácticas operativas adecuadas. Algunas recomendaciones fundamentales son:
- Arranques y paradas controladas: Evitar ciclos térmicos bruscos ayuda a reducir el estrés mecánico y térmico sobre los componentes.
- Evitar sobredemandas: Operar la turbina dentro de sus límites nominales previene sobrecalentamientos o daños por exceso de carga.
- Monitoreo en línea de condiciones: Utilizar sistemas SCADA o software especializados para observar tendencias y anticipar desviaciones de comportamiento.
- Capacitación constante del personal: Los operadores deben estar formados para interpretar señales de falla incipiente y ejecutar maniobras sin afectar la integridad de la máquina.
- Gestión de repuestos críticos: Mantener un stock mínimo de componentes clave para reducir los tiempos de parada ante mantenimiento mayor.
- Registro detallado de eventos y mantenimientos: Llevar una bitácora técnica permite evaluar el historial de la unidad y planificar futuras intervenciones con mayor precisión.
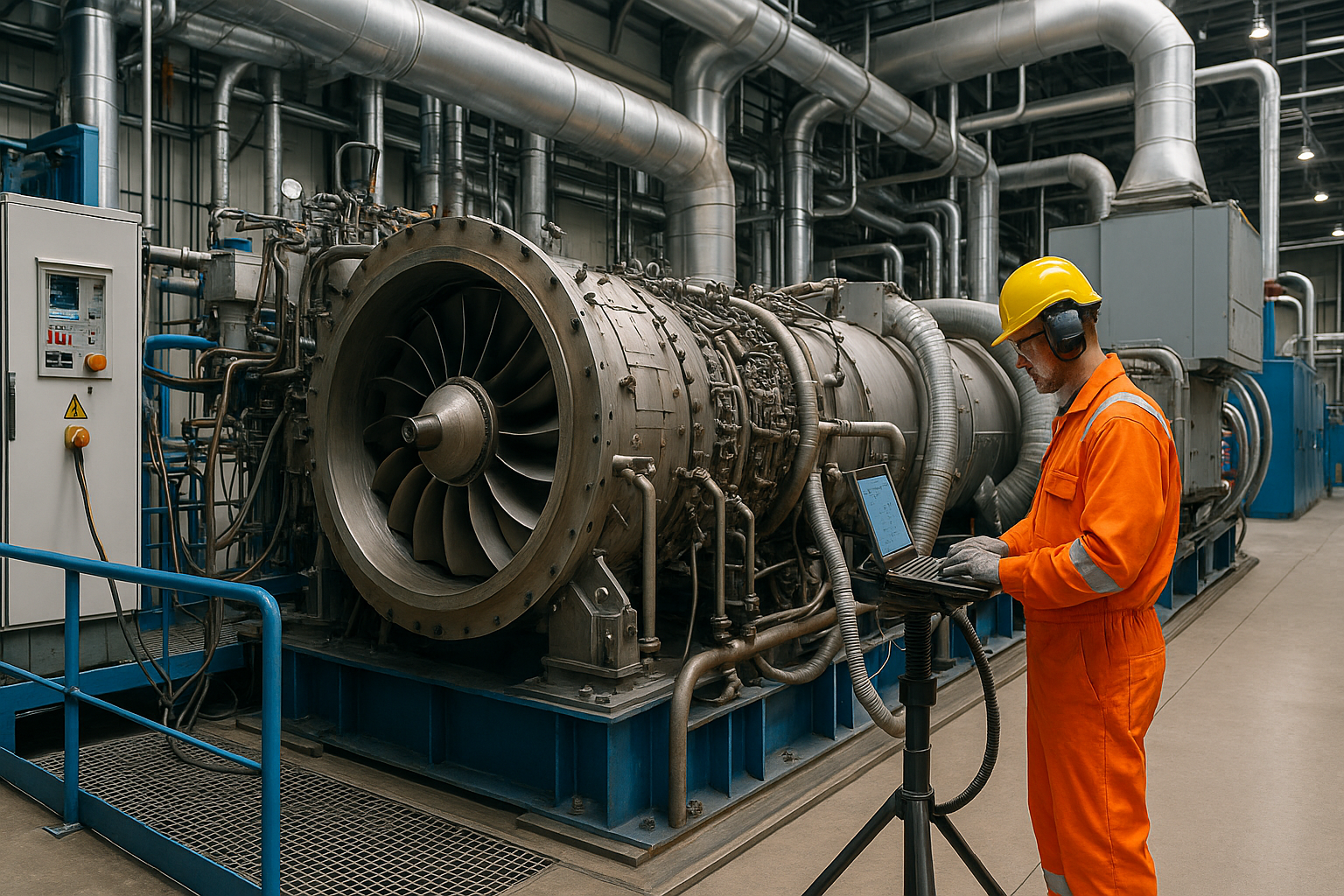
Conclusión
El mantenimiento preventivo en turbinas aeroderivadas no es un gasto, sino una inversión estratégica para garantizar la continuidad operativa, prolongar la vida útil del equipo y reducir los costos de operación. La combinación de cronogramas estructurados, revisión técnica especializada y una operación bien entrenada constituye la base de una gestión eficiente y segura de estos activos energéticos.
En un contexto donde la generación confiable y flexible de energía es cada vez más valorada, las turbinas aeroderivadas juegan un rol protagónico. Asegurar su desempeño mediante buenas prácticas de mantenimiento preventivo es una responsabilidad técnica ineludible para cualquier operador industrial o energético.